事例2.海外拠点から日本への紙袋製品輸送
顧客C=海外自社工場から日本の物流拠点への食品原料輸送のパレット化検討
検討理由
課題①パレット化により積載量が20%減(15段積み⇒12段積み)課題②食品原料輸送に木パレはNG。
ワンウェイ用プラパレは高価すぎる課題③シートパレットの検討では、以下の問題が浮上
1)プッシュプル装置が高価で、全拠点への配備が困難
2)プッシュプル装置の操作が複雑で、リフト運転員に負担を強いる
3)プッシュプル装置付きフォークが専用化するため、増車が必要
リターナブル用樹脂製パスボーダーなら
期待①パスボーダーなら14段積み(7段×2)となり7%減で収まる
期待②パスボーダーは一般のプラパレよりも高価だが、海外への返送コストが10分の1に抑えられるため、
低コスト国際パレット循環が可能となる。
期待③専用フォーク爪により、プッシュプル装置の問題は解消
1)プッシュプル装置の数分の1程度の価格なら全拠点への配備が可能
2)運転員も初めは違和感をもつが、慣れれば大丈夫そうとの感触を得た
3)一般パレットも扱えるのでリフトの稼働維持が可能
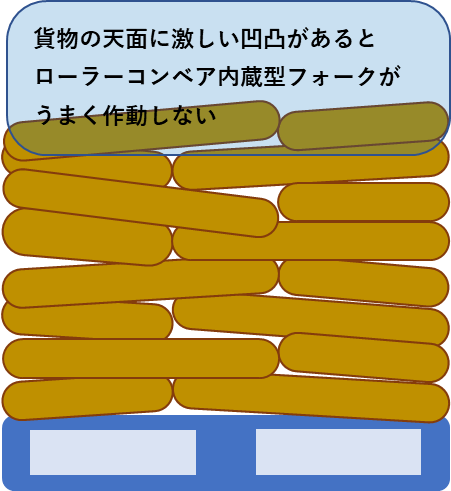
結果)採用に向けて輸送テスト進行中
理由)パスボーダーを上手く使うには、下段側貨物天面の平面性が重要となるが、
同顧客は以下の対応にて問題を克服できると考えている
1)ハイ付けの工夫:海外自社工場の物流現場と協議し、貨物天面の平面性が確保できるよう
現場サイドの協力が得られた。
2)トップカバーの最適化:当初は安価な素材の使い捨てを考えていたが、
作業性を優先し十分な厚みのプラシートに変更。
パスボーダー本体の返送に同梱できるため、コスト回収も見込める。
顧客D=海外別法人からの調達
結果)検討継続
理由)貨物天面の平面性が確保できないため、40ftコンテナ内平積みとするために
1,200㌔/パレットにハイ付けを変更してコスト吸収に努めたが、許容できるコストアップに収まらなかった。
20ftコンテナ内段積みできるようパスボーダーを改良中。